Explore the benefits of local metal fabrication in our latest post, highlighting improved communication, faster delivery, and quality work from firms like Pinnacle Precision.
In the world of metal fabrication, selecting the right manufacturing partner can make or break your projects. Location is a critical factor that is often underestimated.
From fostering strong relationships to ensuring superior quality and timely delivery, the benefits of working with a local metal fabrication company go beyond just convenience.
For the team at Pinnacle Precision, it’s all about forming a strong foundation. We have been the trusted partner for industry-leading companies in Southern California since 1973. With a focus on great service and a fair price, we have been shaping the future of metal fabrication for medical, communications & technology, renewable energy, aerospace and defense.
In this article, we break down the main advantages of choosing a local metal fabricator so you can make a confident choice for your next sheet metal fabrication project partner.

The local advantage
When you work with a local metal fabricator, the kind you’d find when looking for ‘metal fabrication near me,’ the benefits go beyond just convenience, cost and quality work.
Working with local metal fabricators allows for easy communication, quick response times, and streamlined collaboration, ensuring your project progresses smoothly. You can also leverage their deep knowledge of the local market and regional industry & regulations, ensuring compliance with local standards and codes.
Some key advantages of working with a local metal fabricator for your sheet metal work include:
Communication and collaboration:
One of the primary advantages of working with a locally based metal fabrication company is the ease of communication and collaboration. Working with a local company gives you the advantage of face-to-face meetings, on-site visits, and open lines of communication. This facilitates a deeper understanding of your project goals, enabling the fabrication team to provide tailored solutions that meet your precise needs.
Shorter lead times:
By selecting a metal fabrication company that’s based locally, you can streamline the project timeline, mitigate supply chain risks and reduce potential delays. Proximity eliminates logistical challenges, such as long shipping times and potential customs issues, allowing for faster turnaround times.
Furthermore, a local fabricator can better accommodate any unexpected changes or last-minute adjustments, ensuring that your project stays on track and is delivered on time to the exact specifications.
Supporting the local economy:
Choosing a local sheet metal fabrication company also contributes to the growth and development of your local economy. Investing in local businesses fosters job creation and economic stability within your community. This support strengthens the fabricator’s capabilities and helps build lasting relationships based on mutual benefit.
Our core team at Pinnacle includes people that have spent 30-plus years here. Each is committed to helping the next generation learn the intricacies of precision manufacturing and assembly. When you work with trusted local metal fabricators like Pinnacle, you leverage a wealth of local knowledge, experience, and expertise in precision sheet metal fabrication.
The Pinnacle Precision advantage
When you partner with a local metal fabricator like Pinnacle Precision, you’re working with a team dedicated to customer success. Our reputation for precise, durable, and strong metal fabrication solutions comes from 50-plus years of experience partnering with industry-leading companies in the medical, aerospace, defense, communications, technology & information, entertainment, and renewable energy markets.
Our experience extends to fostering and managing a robust supply chain to mitigate risk, enabling us to adhere to tight deadlines and right-in-time delivery schedules.
We don’t follow the standard; we set it, which is why each Pinnacle team member dedicates their workdays to delivering on the promise of a new level of precision.
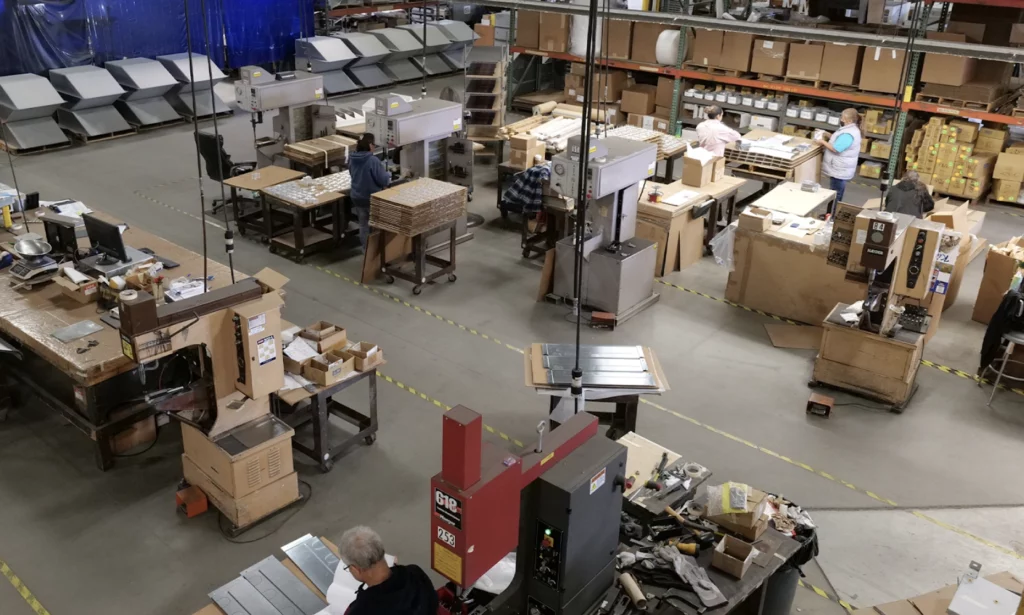
Our world-class facility
Precision, accuracy, and on-time delivery are the things that we stake our reputation on here at Pinnacle. We need industry-leading sheet metal fabrication facilities to deliver on these, and that’s exactly what we’ve got.
The engine of Pinnacle Precision is a 73,000-square-foot facility in Southern California that houses a team of 150 dedicated and experienced manufacturing experts leveraging the power of the latest production tools and decades of experience to manufacture parts that matter. ISO 9001 and AS9100 certified, the plant surpasses industry standards for quality, precision, and accuracy.
Our production floor includes CNC machining, shearing, punching, forming machines, laser cutting equipment, line grainers, and welding stations. Expert leaders and skilled technicians run each station.
The Painting and Silkscreen departments enhance the durability, useability, and appearance of every part coming off the production floor, ensuring our customers can get into production without delay.
A team of support, technical, quality assurance, and management staffers support the plant and constantly seek ways to deliver cost and manufacturing efficiencies to benefit our customers and team.
A diverse range of capabilities
Here at Pinnacle, our reputation is built on experience and excellence from 50-plus years of expert manufacturing crews, meticulous planners and programmers, and quality assurance professionals.
The array of metal fabrication capabilities offered by Pinnacle Precision, include:
Cutting
With a focus on accuracy, while cutting to the tightest tolerances, our production floor boasts a handful of precision CNC laser cutting machines and experienced sheet metal professionals that help set every manufacturing run up for success.
Three flying optics laser-cutting systems with automatic loaders enable our crew to run high-speed production days, resulting in highly accurate sheets cut to the tightest tolerances.
Punching
Blending precision and skill, our Technical and Production teams start every project by leveraging our design and plan expertise to create detailed punch schematics and manufacturing know-how while tooling and running jobs.
With six CNC turret presses that can handle up to 30 tons with up to 40 tool stations per machine, we can punch a variety of sheet metal grades to the tightest tolerances.
Forming
Achieving accuracy and durability in sheet metal parts requires precise bending and forming. At Pinnacle, our Technical team establishes CNC specifications with infinite back gauge and ram settings, while our Production team utilizes our 14 press brakes and extensive tool collection to manufacture parts for industry leaders.
With our wide range of equipment, we are able to deliver high-quality parts on time with the utmost precision.
Machining
With a 73,000-square-foot facility that boasts nine machining centers, we’ve built a reputation for delivering precise parts that last. We use several CNC-powered multi-axis mills to produce sheet metal parts and metal components to the tightest tolerances for a wide range of industries.
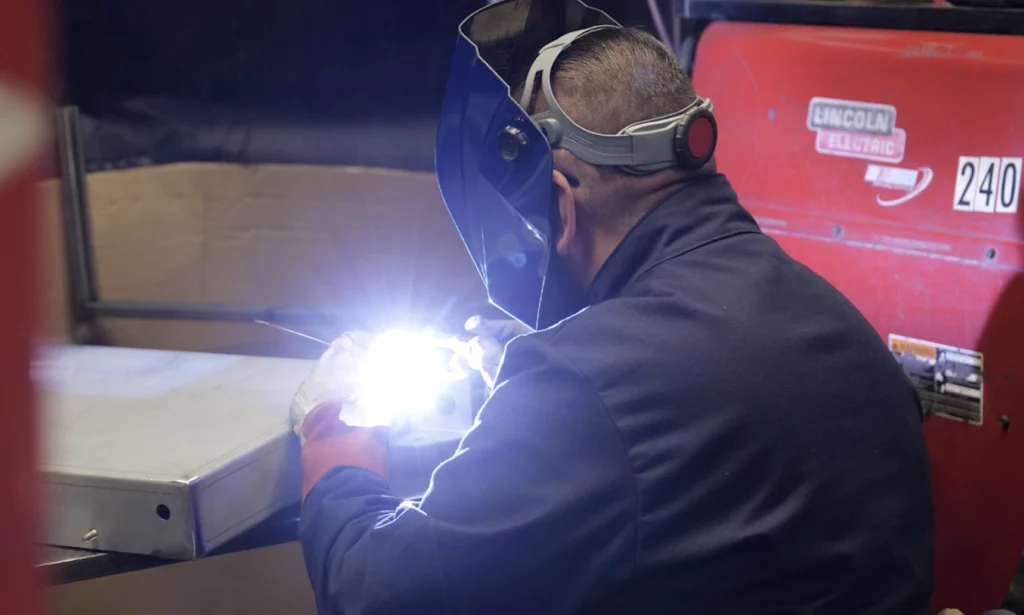
Welding
Our team of certified and experienced welders create assemblies used in essential components, with the skill to weld at the smallest gauges for Class A parts with speed and accuracy.
Our production floor boasts six Arc welding machines, a pair of MIG machines, and six spot welding machines used on sheet metal, aluminum, and stainless steel, welding from 20 gauge up.
Grinding
Preparing sheet metal parts for forming or finishing is essential to delivering high-quality intricate pieces to our customers. Experts in precision grinding, our parts are delivered with clean seams and edges for flawless installation.
We use five vibratory and barrel-type deburring machines, five line grainers, a cyclone bead blast machine, two belt sanders, and six air-operated handheld sanders and grinders for strength, appearance, and durability.
Finishing
Making metal parts pretty and protected from the elements is job number one for Pinnacle’s commercial paint, powder coating, and silkscreening crews.
As one of Southern California’s best sheet metal finishing companies, we use industry-leading materials to enhance the strength, durability, and appearance of every painted part produced here, delivering smooth and textured finishes, powder coatings, and silkscreening projects.
Assembly
Our experienced assemblers have the skill and expertise to take on any challenge that helps speed up the time it takes for you to get a part into production.
Our Assembly experts use semi-automatic presses for thread fastener installations, auto presses with auto feeds, and hardware presses with auto feeds, delivering exactness and precision in applying various seals and installing hardware.
Quality Assurance
Preparing sheet metal parts for forming or finishing is essential to delivering high-quality intricate pieces to our customers. Experts in precision grinding, our parts are delivered with clean seams and edges for flawless installation.
We use five vibratory and barrel-type deburring machines, five line grainers, a cyclone bead blast machine, two belt sanders, and six air-operated handheld sanders and grinders for strength, appearance, and durability.
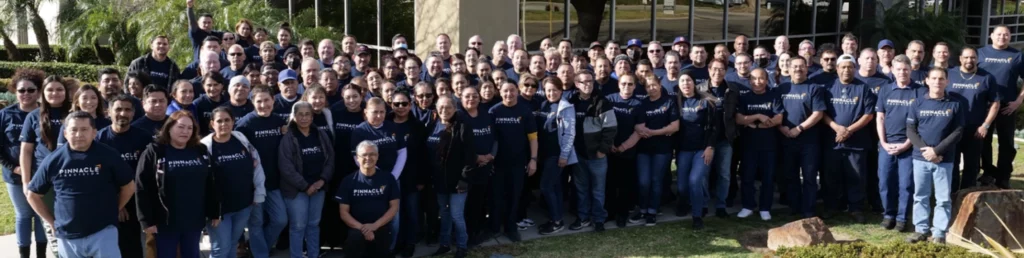
Experience a new level of precision
The advantages of choosing a local metal fabrication company are undeniable. From improved communication and collaboration to enhanced quality control and timely project completion, the benefits speak for themself. Plus, by opting for a nearby fabricator, you can actively participate in the fabrication process, ensuring that your project is executed to your exact specifications.
Next time you require metal fabrication services, consider the advantages of working with a local company like Pinnacle. With a focus on delivering high-quality, on-time parts, we take the time and care to precisely understand what you need as a customer to solve your specific challenges.
Contact us today for a quote.