Innovation in the healthcare industry continues to grow at a rapid pace, increasing the demand for advanced medical solutions. From surgical instruments to diagnostic equipment, complex, highly intricate parts are driving modern medicine, so you need a manufacturing process that ensures precision, quality, repeatability, and versatility.
CNC (Computer Numerical Control) machining has emerged as a proven fabrication process, delivering precision sheet metal parts with tight tolerances that meet the stringent standards required for medical applications.
For over 50 years, Pinnacle Precision has been a trusted partner within the medical manufacturing industry. Our expert team leverages specialized fabrication processes and medical-grade materials to consistently deliver high-quality, precision medical parts that perform in even the harshest environments. With a legacy of precision, collaboration, and quality assurance, we consistently provide manufacturing solutions that meet the strictest medical industry standards.
In this article, we look at how technology is shaping the future of medical care and the reasons why CNC Machining has become the proven process for medical device manufacturing.
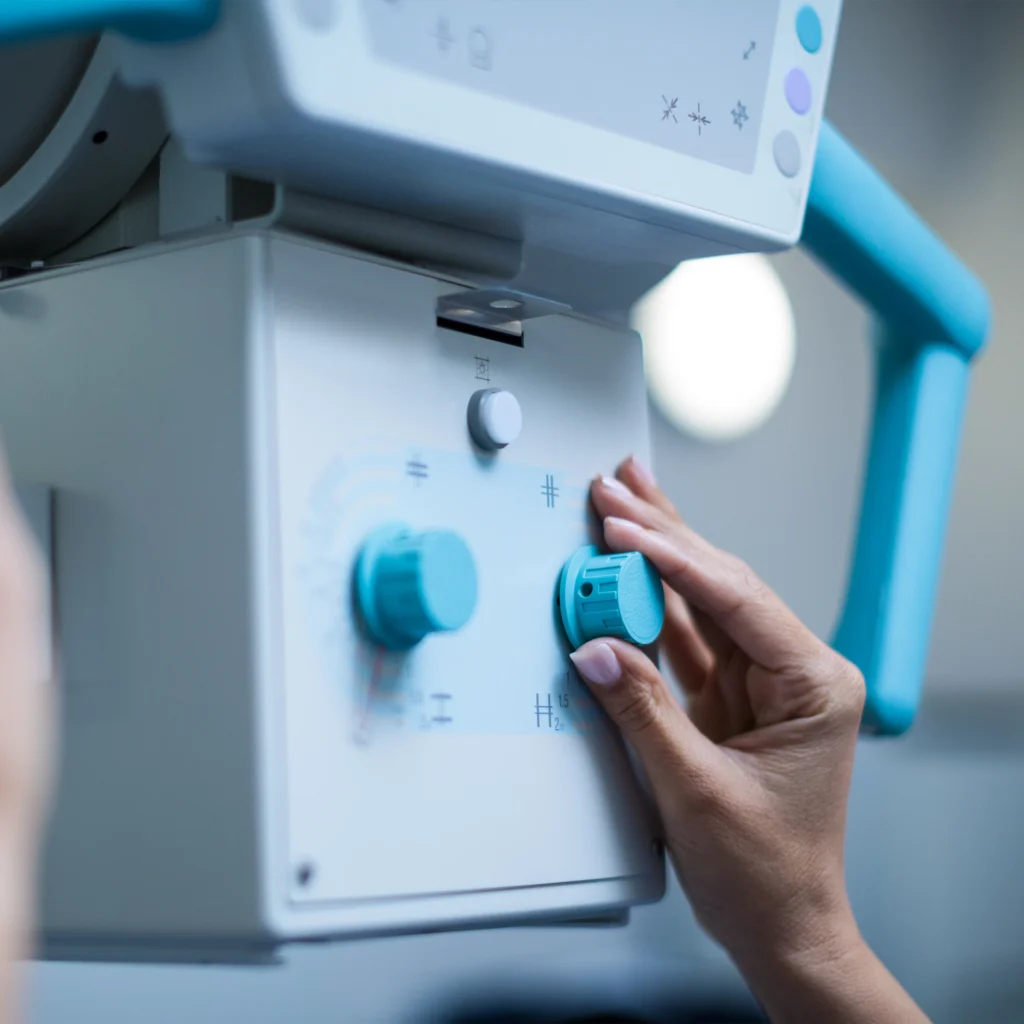
Why CNC Machining is Essential for Medical-Grade Sheet Metal Components
CNC machining has revolutionized medical sheet metal manufacturing thanks to its unique ability to produce complex, highly accurate components.
In an industry where precision and consistency are non-negotiable, even the slightest deviations can compromise a medical device’s functionality, safety, or compliance.
Unlike traditional machining methods, CNC machining provides the highly controlled, repeatable, and scalable manufacturing processes required to meet the stringent quality standards of medical-grade sheet metal components.
Here are some of the main factors that highlight why CNC machining is critical for medical-grade applications:
Precision & Accuracy
Medical devices require extreme precision, with tolerances measured in microns. CNC machining ensures every part meets exact specifications, which is essential for surgical instruments, implants, and other critical healthcare components. The ability to achieve such accuracy minimizes the risk of mechanical failure, enhancing patient safety.
Material Integrity
Medical-grade components must be manufactured from biocompatible, corrosion-resistant materials such as stainless steel, aluminum, and titanium. CNC machining maintains material integrity throughout the fabrication process, ensuring the components withstand sterilization and long-term use in medical environments.
Repeatability & Consistency
CNC machining guarantees uniformity across high-volume production runs. Medical devices and equipment must function reliably in every use, making repeatability a key factor. By leveraging CNC technology, manufacturers can ensure every part meets the same exacting standards, reducing variability and defects.
Speed and Efficiency
CNC machining allows for rapid prototyping and quick production turnaround, reducing design-to-market time significantly. This speed is vital in the medical industry, where timely delivery can impact patient care.
Regulatory Compliance
Medical manufacturing is subject to stringent regulations, including FDA (Food and Drug Administration) and ISO 13485 standards. CNC machining plays a crucial role in ensuring compliance, as it allows for meticulous control over production variables and detailed documentation of manufacturing processes.
With over 50 years of delivering unrivaled partnership and quality, the team at Pinnacle supports the production of cutting-edge medical devices that require exacting standards to protect patients and ensure reliability. Our capabilities empower the industry with innovative solutions that drive progress and improve patient care.
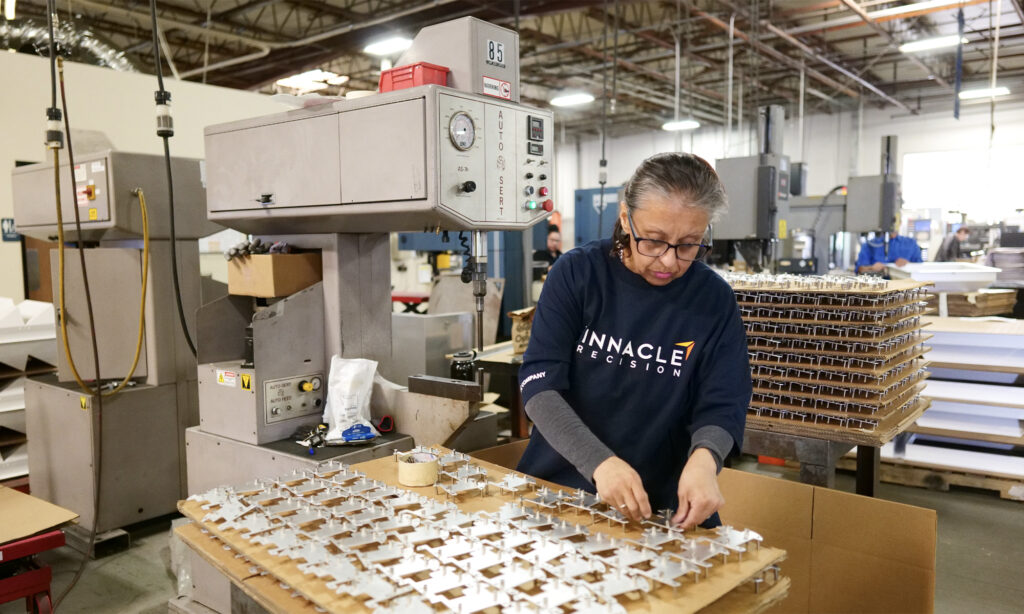
Key Applications in Medical Sheet Metal Manufacturing
With failure putting the health and safety of patients at risk, the medical industry demands high-precision, durable, and biocompatible components that ensure the performance and reliability of healthcare equipment.
Due to its ability to create high-quality precision parts with tight tolerances, CNC machining plays a critical role in the fabrication of complex, high-performance sheet metal components for a wide range of critical medical applications.
One of the primary applications of CNC machining in medical sheet metal manufacturing is the production of surgical tools and instruments. Devices such as scalpels, forceps, retractors, and precision cutting instruments require tight tolerances and smooth surface finishes to ensure optimal performance and sterility. The precise machining process ensures that these tools are crafted with high accuracy and repeatability, providing surgeons with reliable instruments for delicate procedures.
Some of the other key applications of CNC machined components include:
Medical Equipment Enclosures
CNC-machined sheet metal enclosures house sensitive imaging, diagnostic, and treatment devices. These enclosures must be both durable and precisely engineered to protect delicate medical electronics.
Brackets & Mounting Components
Support structures and brackets for medical technology require robust and precise manufacturing to ensure stability and longevity. CNC machining enables the production of intricate mounting components that meet strict industry standards.
Custom Precision Panels & Frames
Support structures and brackets for medical technology require robust and precise manufacturing to ensure stability and longevity. CNC machining enables the production of intricate mounting components that meet strict industry standards.
Sterile & Corrosion-Resistant Parts
Medical environments demand sterile and corrosion-resistant components. CNC machining allows for the fabrication of sheet metal parts with specialized coatings and finishes that maintain sterility and withstand harsh cleaning procedures.
At Pinnacle Precision, we specialize in fabricating high-quality, precision-machined medical sheet metal components tailored to meet the evolving needs of the healthcare industry. By leveraging state-of-the-art CNC machining technology, we ensure that every component is engineered for durability, precision, and reliability, making us a trusted partner in medical sheet metal manufacturing.
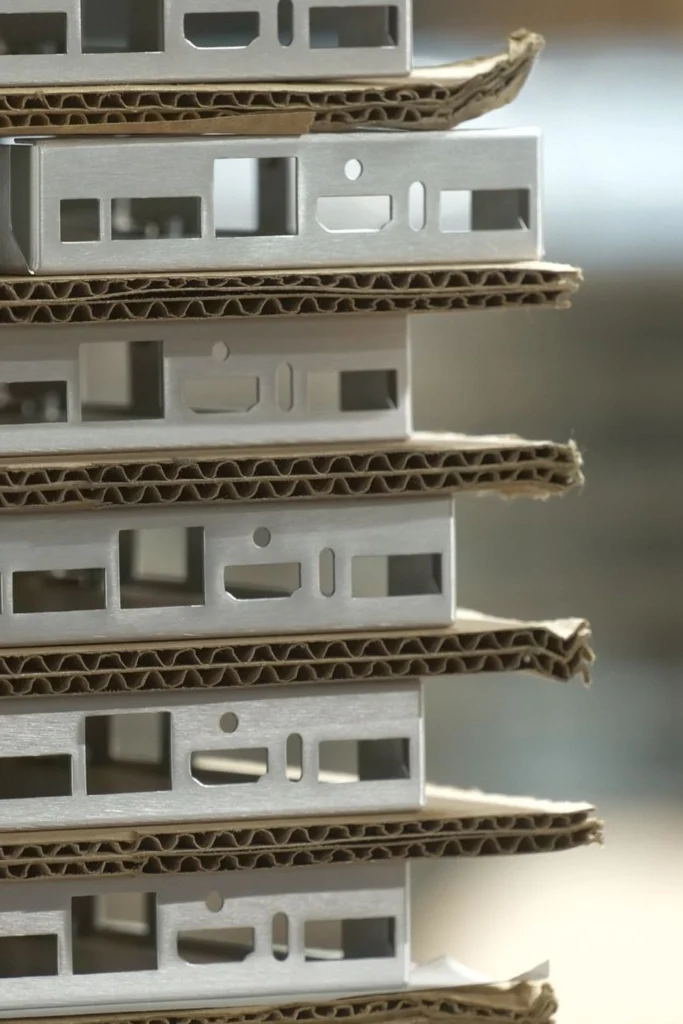
Advantages of CNC Machining for Medical Sheet Metal Over Other Methods
CNC machining offers several distinct advantages compared to traditional fabrication methods like stamping, laser cutting, and forming.
One of the major benefits of CNC machining is design flexibility. While traditional fabrication methods are often limited to simpler geometries and standard shapes, CNC machining allows for complex, custom designs with intricate details, internal cavities, and multi-axis cutting. This is particularly advantageous for customized implants, surgical tools, and diagnostic equipment, which require precise, patient-specific modifications that stamping or forming cannot achieve.
Other key advantages of CNC machining include:
- Unmatched Precision – CNC machining delivers superior accuracy, which is essential for medical devices that must adhere to strict tolerances.
- High Repeatability – Ensures identical production of components, reducing variability and enhancing device reliability.
- Material Versatility – CNC machining accommodates biocompatible metals and advanced plastics, allowing for diverse medical applications.
- Customization – Enables the production of personalized implants, prosthetics, and device components tailored to specific patient needs.
- Reduced Material Waste – CNC machining optimizes material usage, minimizing waste and lowering costs without compromising quality.
CNC machining also provides superior surface finish quality compared to traditional cutting or stamping methods. Medical components often require smooth, burr-free edges and polished surfaces to minimize contamination risks and improve sterilization efficiency. CNC machining ensures a high-quality finish without the need for excessive post-processing, making it ideal for biocompatible metal components that must maintain strict hygiene standards.
At Pinnacle Precision, we leverage state-of-the-art CNC machining technology to produce high-precision medical sheet metal components with unmatched accuracy, durability, and compliance.
The Importance of Quality Assurance in Medical Manufacturing
The medical industry has some of the most stringent quality control measures in manufacturing, and for good reason. Even the slightest defect in a medical component can have life-altering consequences.
At Pinnacle Precision, quality assurance is embedded in every stage of production.
With a robust quality management system in place, we ensure adherence to key standards such as ISO 13485 and FDA requirements, guaranteeing that every part we produce meets stringent safety and quality guidelines.
How Pinnacle Ensures Compliance with Standards
Multi-Stage Inspections
At Pinnacle Precision, quality assurance is embedded in every stage of the manufacturing process. Unlike many metal fabrication companies, our production floor is staffed with experienced professionals—many with decades of expertise—who understand the importance of accuracy and precision.
The Quality Assurance team actively inspects components as they move through the facility, partnering with the Technical and Production crews to ensure compliance with exact specifications. To maintain the highest level of accuracy, we utilize precision measuring tools, including calipers, micrometers, and an array of gauges—pin, GO/NO GO, height, depth, radius, and surface roughness. We also use paint chips to match coatings precisely to customer requirements.
Additionally, Pinnacle boasts a laser rapid inspection system, capable of measuring the finest details, dimensions, and tolerances. This advanced technology ensures that every part—especially those used in life-saving medical applications—meets the strictest quality standards before leaving our facility.
Precision Measuring Tools
We use advanced tools like Coordinate Measuring Machines (CMM) to ensure every part we produce meets the exact specifications required.
Material Traceability
We maintain full material traceability and documentation, ensuring all components meet regulatory standards and allowing for seamless reporting when needed.
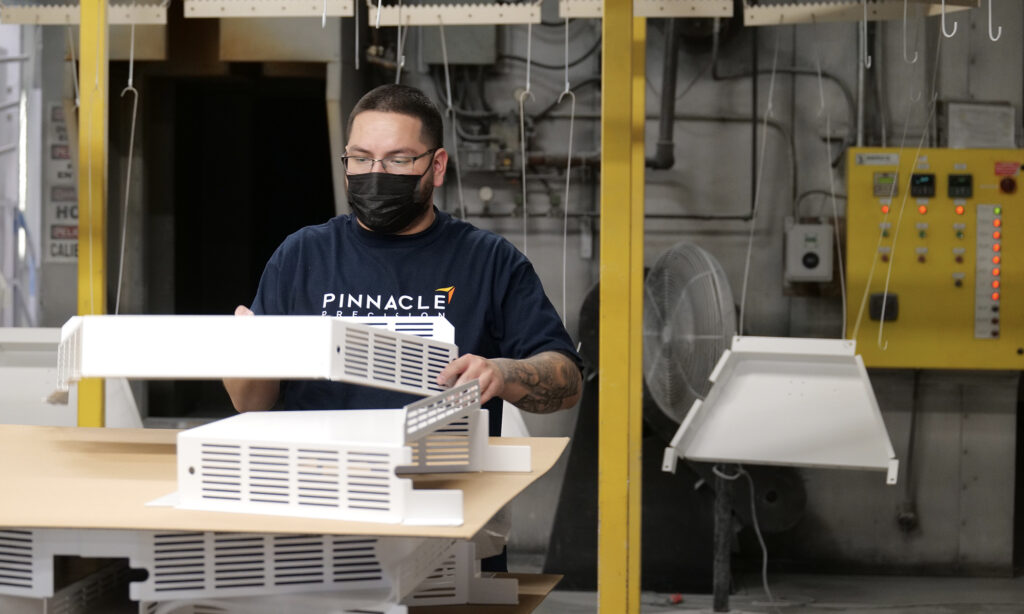
The Critical Role of Material Selection for Medical CNC Machining
Material selection in Medical CNC Machining is a pivotal factor that directly impacts the safety, functionality, and longevity of medical devices.
The choice of material is not merely a design decision but a critical determinant of a device’s performance and patient safety. Medical components must withstand harsh sterilization processes, bodily fluids, and mechanical stress, making material properties such as biocompatibility, corrosion resistance, strength, and wear resistance essential considerations.
For instance, implantable devices require materials that are not only strong but also biologically inert to prevent adverse reactions within the body. Titanium and its alloys, widely used in orthopedic and dental implants, offer exceptional biocompatibility, lightweight strength, and corrosion resistance, ensuring long-term stability. Stainless steel, on the other hand, is frequently chosen for surgical instruments and orthopedic tools due to its high durability, resistance to oxidation, and ability to endure repeated sterilization cycles.
Beyond functionality, the machinability of a material plays a significant role in ensuring precision and efficiency during production. Some materials, while offering superior biocompatibility, can be challenging to machine, requiring advanced CNC machining techniques, specialized tooling, and strict process control to maintain tight tolerances and surface finishes critical to medical applications.
As medical machining specialists, the team at Pinnacle Precision understands that choosing the right material isn’t just about performance—it’s about ensuring biocompatibility, corrosion resistance, and mechanical integrity under demanding conditions.
From stainless steel for surgical instruments to titanium implants, each material must be carefully analyzed for its strength, durability, and compatibility with the human body. Our expertise in machining these high-performance metals and alloys allows us to produce precision medical components that meet strict regulatory and quality standards. With our advanced medical machining services, we deliver reliable, high-precision solutions that medical professionals trust for life-saving applications.
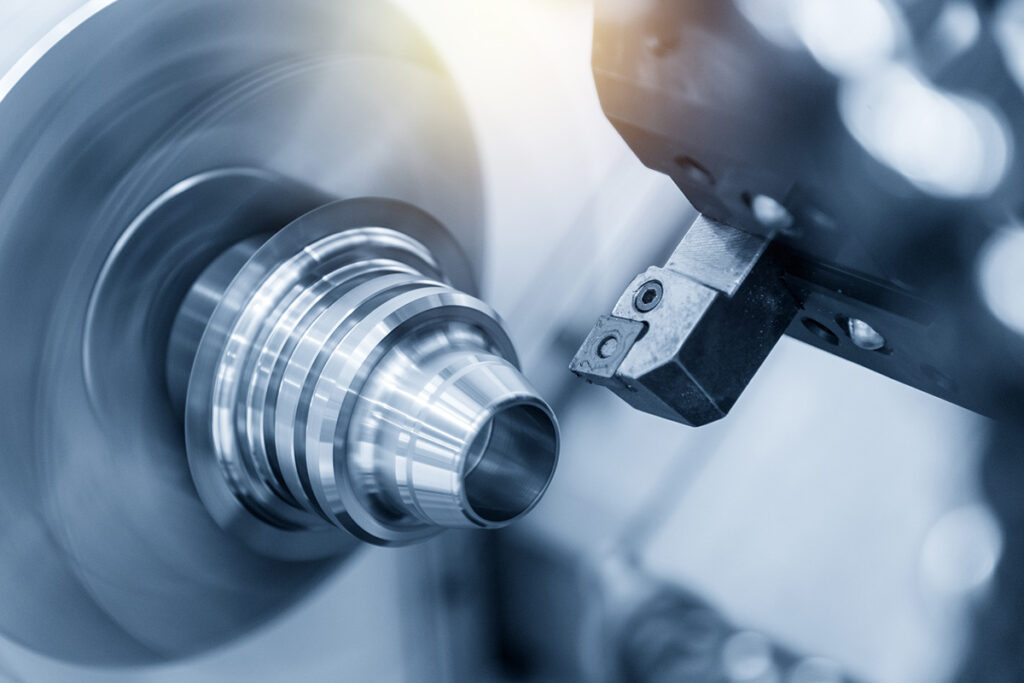
Pinnacle Precision’s Expertise in CNC Medical Machining
At Pinnacle Precision, we recognize the fast-paced and evolving nature of medical manufacturing. Our commitment to precision, innovation, and collaboration ensures we deliver top-quality CNC-machined components for the medical industry.
As a trusted partner for leading medical manufacturers, we’ve been delivering precision machining for the medical industry for over 50 years.
Leaders in medical device manufacturing, we’ve built a reputation for a relentless commitment to manufacturing the highest quality, precise components that perform in even the most demanding medical environments.
What sets Pinnacle Precision apart:
CNC-Powered
The Technical and Production teams at Pinnacle Precision leverage the power and accuracy of CNC machines to deliver the high quality and consistency demanded in the medical industry.
Pinnacle’s investment in the latest CNC tools, including 5-axis machining centers, enables us to meet the most stringent quality standards while ensuring efficient and cost-effective production processes of complex metal parts and components.
Advanced CNC Capabilities
The 73,000-square-foot production floor at Pinnacle Precision features CNC-powered machines that enable the accurate manufacturing of complex parts, components, and assemblies.
Pinnacle’s investment in the latest CNC machining technology, including large 5-axis centers, enables us to meet the most stringent quality standards while ensuring efficient and cost-effective production processes of complex metal parts and components.
Medical-Grade Alloys & Finishes
We boast decades of experience working with stainless steel, aluminum, titanium, and specialized coatings for medical applications.
Finishing is essential to producing durable parts, components, and assemblies used in medical devices. Pinnacle’s finishing crew includes commercial paint, powder coating, and silkscreening experts. Each person leverages meticulous processes and techniques to produce smooth surfaces, precise dimensions, and impeccable aesthetics for medical components and devices.
Regulatory Compliance & Quality Assurance
Every member of the Pinnacle team understands the importance of quality assurance, ensuring every part meets the highest industry standards for safety and reliability.
Our people study medical regulatory requirements and implement strict inspection and testing procedures on the production floor.
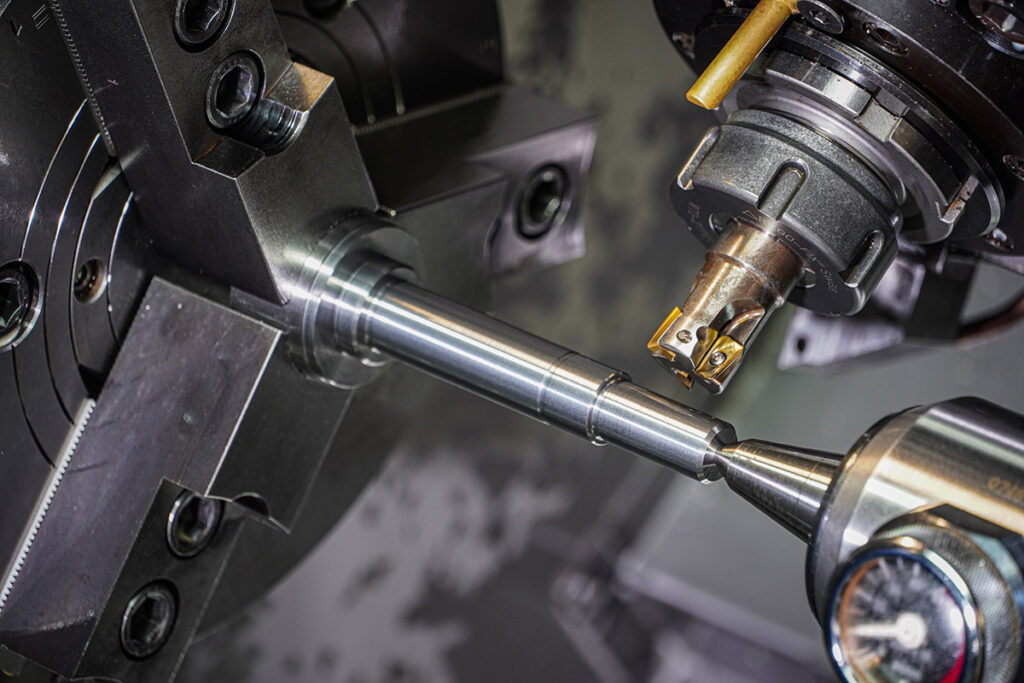
Leading the Way in Medical Manufacturing
With modern medical technology evolving at record speed, the demand for suppliers that can deliver high-quality, compliant, and innovative solutions is only set to grow.
The reliance on proven fabrication processes like CNC machining is set to grow due to its ability to manufacture high-precision, regulation-compliant sheet metal components that can perform reliably and safely in a range of critical medical device applications.
As a trusted partner in medical manufacturing, Pinnacle Precision delivers CNC-machined medical components that meet the highest industry standards. Operating with a communication-first mantra, we’re here to collaborate and tackle your manufacturing needs with innovation, precision, and quality.
Whether you need precision enclosures, brackets, or sterile medical parts, our expertise ensures top-quality manufacturing tailored to your needs. If you need precision CNC machining for medical industry applications, you can rely on the team at Pinnacle.
Contact Pinnacle Precision today to discover how we can help deliver precision and expertise for your medical manufacturing project.