Achieving Tight Tolerances with Precision CNC Metal Parts Processing
In advanced metal manufacturing, achieving tight machining tolerances is more than a technical requirement — it’s a critical performance standard.
Whether you’re manufacturing a component for an aircraft engine, a surgical implant, or an industrial robotic assembly, tight tolerances ensure that each part performs reliably, even in the harshest environments.
As a leading provider of CNC machining and metal fabrication solutions, Pinnacle Precision specializes in producing high-accuracy metal components for industries that demand the highest levels of craftsmanship, reliability, and compliance. With deep expertise in CNC milling, turning, and multi-axis machining, our expert team delivers innovative, cost-effective solutions to some of the most complex manufacturing challenges.
In this article, we explore how advanced CNC machining enables the production of metal components with tight tolerances, the importance of precision in key industries, and how Pinnacle Precision sets the standard for accuracy, consistency, and performance.
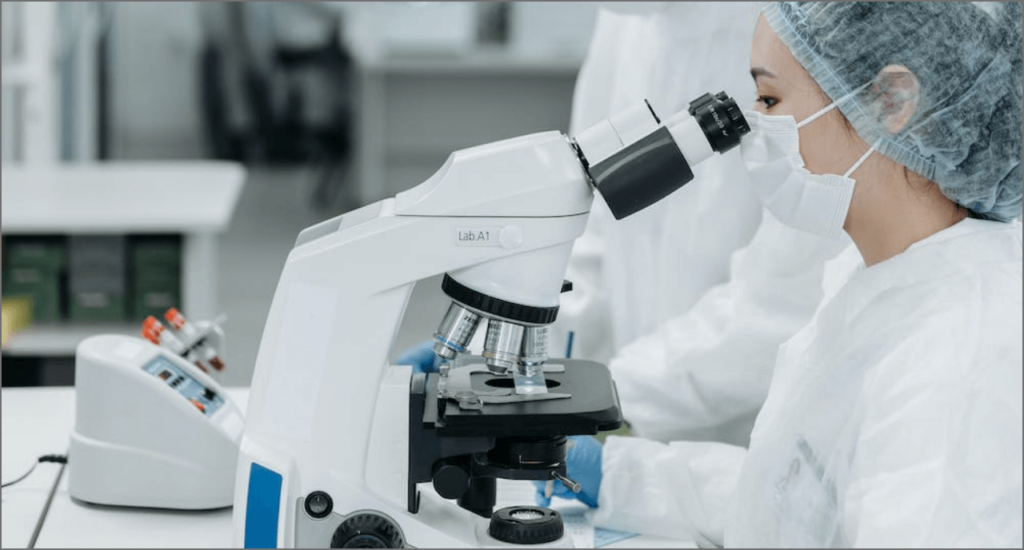
Why Tight Tolerances Matter in Aerospace, Medical, and Industrial Applications
In high-stakes industries like aerospace, medical, and industrial manufacturing, a deviation of even a few micrometers can compromise an entire system’s functionality, safety, and reliability. Meeting precise tolerance requirements is critical to ensuring that each component integrates seamlessly into larger assemblies and performs under extreme conditions.
In aerospace, structural integrity and aerodynamic performance depend on the exact fit between parts. Components such as turbine blades or airframe brackets often require bilateral tolerances to maintain precise symmetry and balance, ensuring stability and safety during flight.
Tight tolerances in medical devices ensure the accuracy and effectiveness of surgical tools and implants used in life-saving procedures, where even slight discrepancies can affect patient outcomes.
When we talk about the industrial and automotive sectors, maintaining standard tolerances or exceeding them is essential to ensure proper gear meshing, shaft alignment, and housing fits — critical for minimizing wear, maximizing efficiency, and preventing costly equipment failures.
The Role of CNC Machining in Achieving Extreme Precision
Computer Numerical Control (CNC) machining has revolutionized the ability of manufacturers to achieve tight tolerances in their metal components. By automating the machining process and enabling incredibly fine control over tool paths and material removal, the innovative process makes it possible to deliver intricate geometries to sub-micron accuracy. This level of precision is fundamental to producing CNC machined parts that need to meet stringent dimensional and geometric requirements.
The introduction of multi-axis machines, high-speed spindles, and real-time feedback systems has further expanded the capabilities of precision machining, allowing for greater flexibility and accuracy when handling complex components. Advanced systems can consistently meet strict CNC machining tolerances, often achieving deviations within a few microns. These tight limit tolerances are essential in ensuring that parts fit together perfectly, perform reliably under stress, and comply with industry-specific standards.
Whether it’s producing aerospace brackets, surgical components, or high-performance industrial parts, modern CNC technology enables manufacturers to push the boundaries of precision while maintaining repeatability across production runs.
Advancements in CNC Technology Enhance Accuracy and Repeatability
Today’s CNC machines are equipped with cutting-edge software, sensors, and control systems that dramatically improve repeatability and accuracy. With real-time compensation for thermal expansion, tool wear, and material inconsistencies, modern CNC systems consistently deliver parts that meet the strictest dimensional and geometric tolerances.
These technological advancements have also refined core manufacturing processes, enabling tighter control over every stage of production. High-precision cutting tools, particularly sharp cutting tools made from advanced carbide or coated materials, play a critical role in achieving clean cuts, fine surface finishes, and minimal dimensional deviation. By optimizing tool paths and leveraging data-driven machining strategies, manufacturers can reduce cycle times while maintaining exceptional accuracy across multiple production runs.
Key Benefits of High-Precision CNC Machining
High-precision CNC machining offers unmatched accuracy, enabling the production of complex metal components with tolerances measured in microns. This level of precision ensures superior part performance, repeatability across production runs, and optimal material efficiency — making it essential for high-stakes industries like aerospace, medical, and advanced manufacturing.
The key benefits of high-precision CNC machining include:
Unmatched Accuracy: Achieving Micrometer-Level Precision
Modern CNC machining can achieve tolerances within ±0.001 inches — or even tighter in some applications. This level of accuracy is vital for components used in high-speed, high-load, or high-stress environments, where any deviation could lead to failure. Pinnacle Precision uses advanced multi-axis CNC machines and real-time feedback systems to ensure every cut, hole, and surface meets exacting specifications.
Improved Performance & Reliability
Tight tolerances contribute directly to mechanical efficiency, system integrity, and operational reliability. In engines, hydraulic systems, and medical devices, consistent clearances and precise fits help reduce friction, prevent leaks, and ensure reliable performance over time. CNC machining allows Pinnacle to maintain these critical specifications across every component they produce.
Material Efficiency
Precision CNC machining minimizes material waste by enabling optimal tool paths and reducing the need for secondary operations or rework. This efficiency not only reduces costs but also ensures that high-value materials — such as titanium or Inconel — are used as effectively as possible, which is particularly important in aerospace and medical manufacturing.
Scalability & Repeatability
High-precision CNC machining ensures that once a part is perfected, it can be reproduced with exacting accuracy across hundreds or thousands of units. This scalability is key for OEMs and manufacturers who require consistent performance across multiple assemblies or production runs. Pinnacle Precision’s process controls and quality assurance systems guarantee identical results every time.
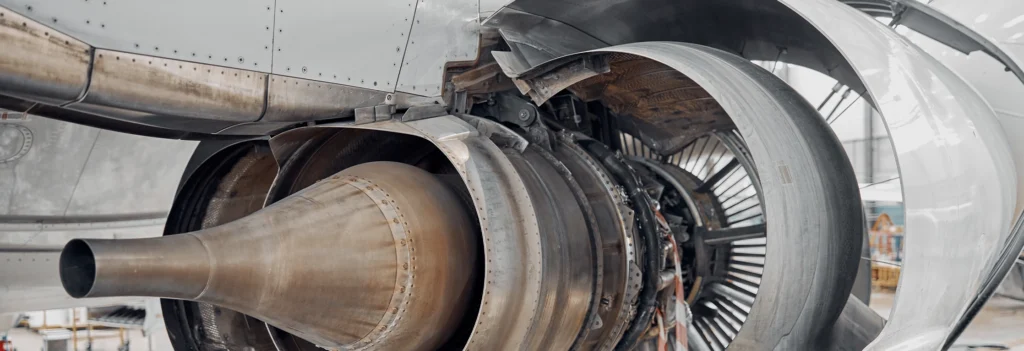
Industries That Rely on Tight Tolerances
Here are some of the key sectors where precision isn’t just preferred; it’s mission-critical.
Aerospace
Aerospace is perhaps the most demanding industry when it comes to tight tolerances. Flight-critical components like turbine blades, engine housings, and structural brackets must be manufactured to the highest standards to ensure safety, fuel efficiency, and aerodynamic performance. Even microscopic deviations can lead to stress concentrations or imbalances that jeopardize an entire aircraft system.
Pinnacle Precision has extensive experience working with aerospace-grade materials and adhering to AS9100 standards. Our advanced CNC machining capabilities support the production of high-strength, lightweight components that meet the rigorous specifications of aerospace applications.
Medical
In the medical field, the margin for error is virtually nonexistent. Devices such as orthopedic implants, dental fixtures, and surgical instruments require perfect symmetry, precise fits, and flawless finishes to perform safely and effectively.
Here at Pinnacle, our expert team partners with leading medical manufacturers to deliver precision CNC machining solutions that perform in even the most testing environments. Our cleanroom-compatible processes and biocompatible material expertise ensure that every part produced is suitable for sensitive, life-critical applications.
Industrial & Automotive
From robotic assemblies to precision gears and electronic enclosures, industrial and automotive applications demand consistency, durability, and fit. Improper tolerances can result in premature wear, energy inefficiencies, or system failures.
Pinnacle has built a reputation for delivering high-volume, high-precision parts for these industries, optimizing every design for manufacturability while maintaining superior accuracy and strength.
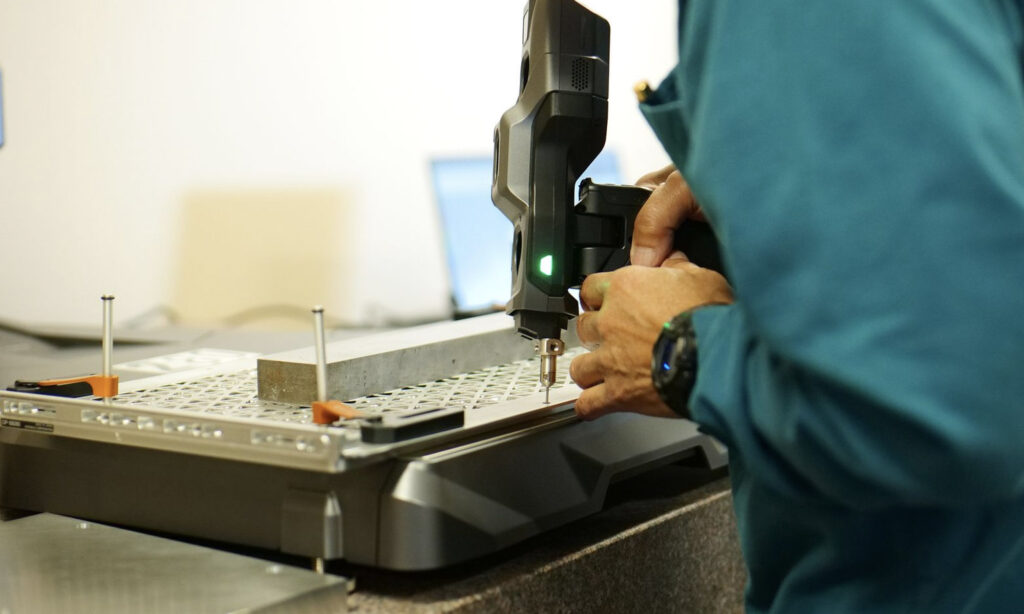
How Pinnacle Precision Achieves Unrivaled Accuracy
Here at Pinnacle Precision, we believe that excellence in CNC machining isn’t just about having the right equipment – it’s about integrating advanced technology, material expertise, and process control to achieve the highest standards in metal part production.
Here’s what sets Pinnacle apart:
State-of-the-Art CNC Technology
Our 73,000-square-foot advanced manufacturing facility boasts an arsenal of industry-leading CNC machines, including:
- 5-Axis and Multi-Axis Machining Centers: These machines can access complex angles and surfaces without repositioning the part, allowing for more accurate and efficient machining of intricate geometries.
- Electrical Discharge Machining (EDM): Ideal for machining hard metals and fine features with extreme precision.
- Laser Measurement Systems: Integrated into the production workflow, these systems verify dimensions in real-time, ensuring each component remains within tolerance.
These technologies allow us to produce complex parts with extreme dimensional accuracy and surface finish quality.
Material Expertise
Working with a wide variety of metals — from stainless steel and aluminum to exotic alloys like titanium and Inconel — requires a deep understanding of how different materials respond to heat, force, and machining speed.
Our skilled team of machinists and engineers tailor each machining strategy to the material’s properties to prevent deformation, reduce tool wear, and maintain tolerances even on the most challenging components.
Rigorous Quality Control
Precision is only as good as its verification. At Pinnacle, we maintain strict quality control protocols and aim to exceed industry standards and customer expectations while delivering essential parts at just the right time.
Our certifications include:
-
- AS9100D: Aerospace Quality Management
- ISO 9001:2015: General Manufacturing Quality
- ITAR: Defense-related articles or services
- RoHS: Restriction of Hazardous Substances
Advanced metrology equipment, such as coordinate measuring machines (CMMs), optical comparators, and surface roughness testers, are used throughout the production process to validate and document every dimension.
Custom Engineering Solutions
No two manufacturing challenges are the same, so we work closely with our clients to develop tailored machining strategies based on part geometry, function, material, and production volume. From DFM (Design for Manufacturability) consultations to prototype development and full-scale production, we offer a complete suite of engineering support services.
Our collaborative approach ensures each solution is optimized for cost, efficiency, and quality—without compromising on tolerances.
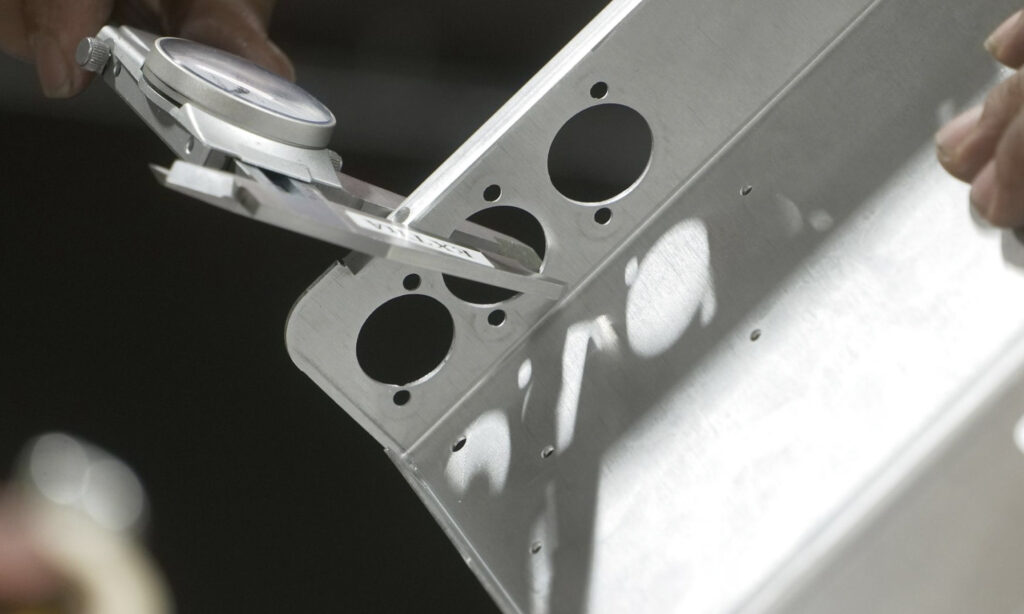
Ensure the Reliability and Functionality of Your High-Performance Components
Precision CNC machining is more than a method; it’s a critical enabler of innovation, safety, and performance in today’s most demanding industries. More than just a goal to aim for, achieving tight tolerances is essential to producing high-performance components that function flawlessly under stress, heat, and movement.
If you’re looking to push the boundaries of engineering and design, the expert team at Pinnacle Precision is here to help. We boast advanced CNC capabilities, material expertise, and uncompromising quality control and deliver thousands of precision-engineered components daily. Whether you’re in aerospace, medical, or industrial manufacturing, we provide the consistent precision you need to compete at the highest level.
Let Pinnacle Precision be your partner in achieving the highest levels of accuracy, reliability, and efficiency in CNC metal parts processing.